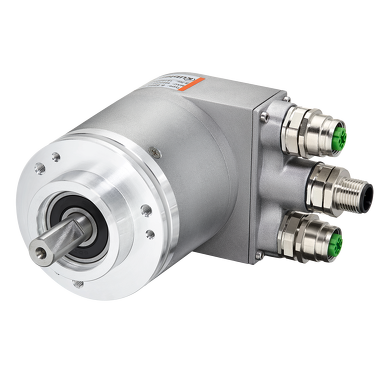
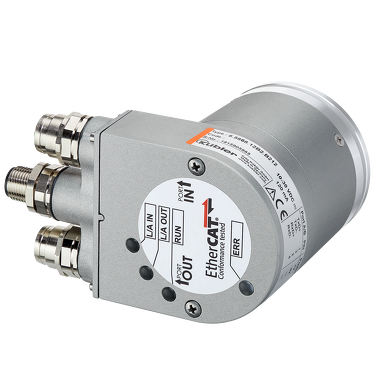
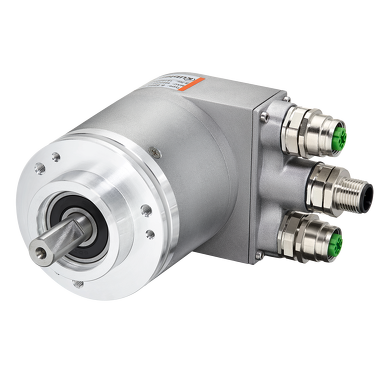
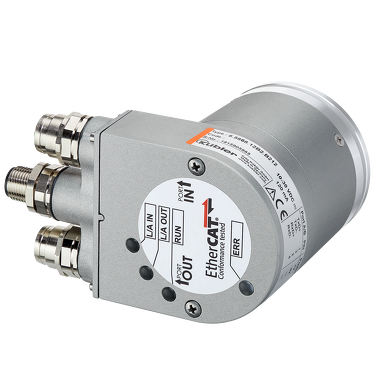
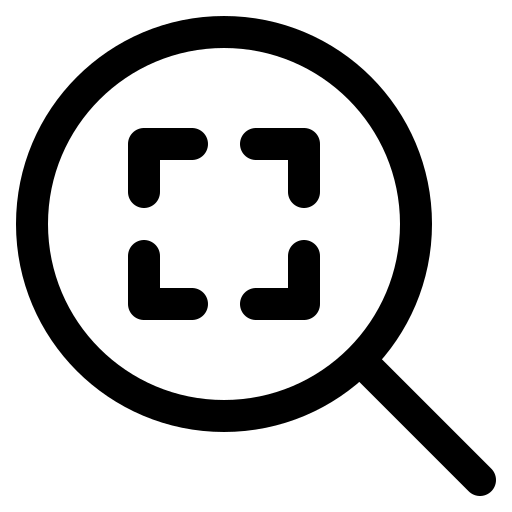
Encoders Absolute multiturn
Sendix 5868
|
|


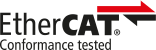
For real-time communication: Industrial Ethernet encoders with EtherCAT interface.
The absolute encoders Multiturn Sendix 5868 / 5888 with 2nd-generation EtherCAT interface and optical sensors can be used in all applications with EtherCAT technology. The data communication is based on CAN over EtherNet and is ideally suited for real-time applications. These encoders are available with shafts up to a maximum diameter of 10 mm or as blind hollow shafts up to 15 mm.
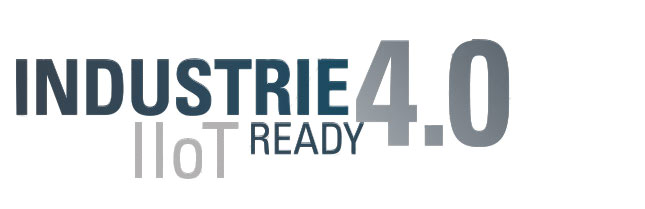
Connectivity stands for the ability to communicate additional information and / or to be integrated in a network. This can take the form of additional interfaces such as OPC-UA (e.g. for additional edge communication) or Industrial Ethernet communication as well as a digital interface such as "BISS" or "SCS open link".
Identification is the ability to transmit technical information by means of an electronic data sheet / type plate. In addition, further information about the machine can be transmitted (e.g. information about the axis where the encoder is installed). Essentially, all the information required in the application for asset management is recorded here.
Mechanical | |
---|---|
Dimension | Ø 58 mm |
Shaft type |
6 mm shaft, with flat surface 10 mm shaft, with flat surface 1/4 " shaft, with flat surface 3/8 " shaft, with flat surface |
Flange type |
Synchro flange / Servo flange Clamping flange Square flange Ø 58.00 mm |
Working temperature | -40 °C ... +85 °C |
Protection level |
IP65 IP67 |
Connection types |
M12 connector radial |
Max. rotational speed |
9.000 min-1 |
Weight | 540 g |
Electrical | |
---|---|
Scanning | optical |
Resolution max. |
16 bits singleturn 12 bits multiturn |
Power supply |
10...30 V DC |
Interfaces |
EtherCAT |
- EtherCAT conformance tested.
- Integration of the latest slave – EtherCAT stack from Beckhoff, Version 5.01.
- Ideally suited for use in harsh outdoor environments, thanks to IP67 protection and rugged housing construction.
- Use of CoE (CAN over EtherNet).
- Genuine new position information as a result of minimal cycle time of 62.5 μs in the DC mode.
- Faster, easier error-free connection thanks to M12 connectors.
- Supports Hot Connect.
Accessories
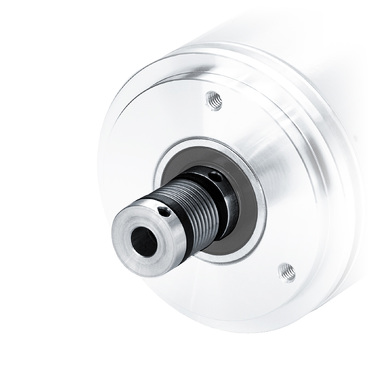
Bellows coupling
Bellows couplings are used for the cost-optimized connection of motor and encoder. In addition, a correction of angular errors between drive and encoder is achieved. Compensation for larger axial errors.Bellows coupling (stainless steel).
8.0000.1102.XXXX |
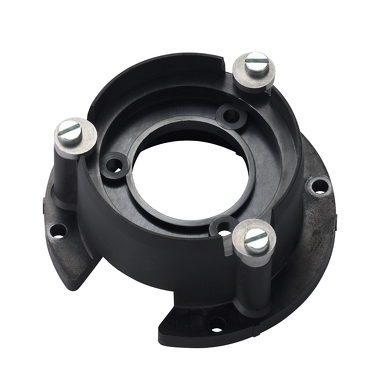
Assembly bell
For shaft encoders with flange ø 50 ... 58 mmFast encoder mounting. Electrical and thermal insulation through glass-fibre reinforced plastic and insulating spring washer coupling - complete delivery as a set.
Scope of delivery
- Mounting bell
- Spring washer coupling (8.0000.1401.XXXX)
- Mounting eccentric (8.0000.4B00.0000)
- Mounting accessories
8.0000.4500.XXYY |
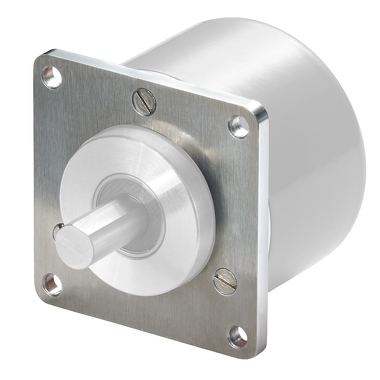
Adapter flange, square, 4 mm
For shaft encoders with clamping flange ø 50 ... 58 mmScope of delivery
- Flange adapter (aluminium)
- 3 screws for mounting on the encoder
Connection to the application (not included in delivery)
- 4 screws
58,0 mm x 4 mm | 8.0010.2100.0000 |
63,5 mm x 3 mm | 8.0010.2120.0000 |
70,0 mm x 10 mm | 8.0010.2600.0000 |
80,0 mm x 4 mm | 8.0010.2800.0000 |
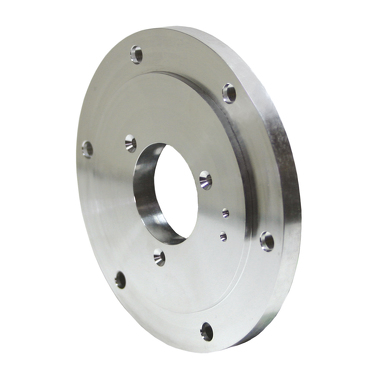
Flange, Ø 115mm Euroflange
For shaft encoders with flange ø 50 ... 58 mmScope of delivery
- Flange adapter (aluminium)
- 3 screws for fastening to the encoder
Connection to the application (not included in delivery)
- 6 screws
Drehgeber 580x/5000 | 8.0010.2160.0000 |
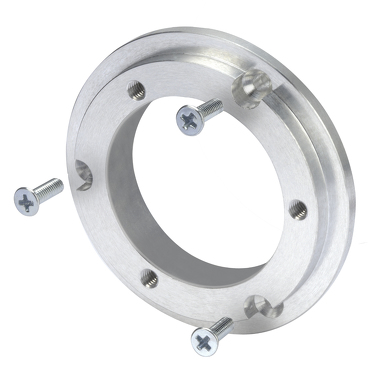
Flange, Ø 58mm
For shaft encoders with flange ø 50 ... 58 mmAdapter for converting a clamping flange into a synchro flange.
Scope of delivery
- Flange adapter (aluminium)
- 3 screws for mounting on the encoder
Connection to the application (not included in delivery)
- 3 screws
8.0010.2180.0000 |
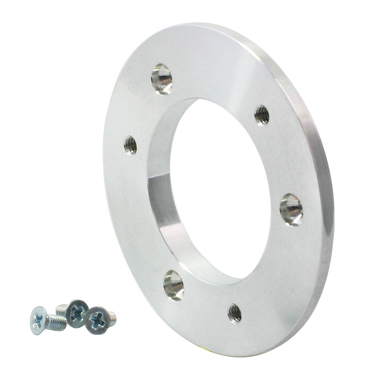
Flange, Ø 65mm
For shaft encoders with flange ø 50 ... 58 mmWith this flange adapter, Kübler encoders of size 58 mm can replace third-party encoders of size 65 mm.
Scope of delivery
- Flange adapter (aluminium)
- 3 screws for mounting on the encoder
Connection to the application (not included in delivery)
- 3 screws
8.0010.2230.0000 |
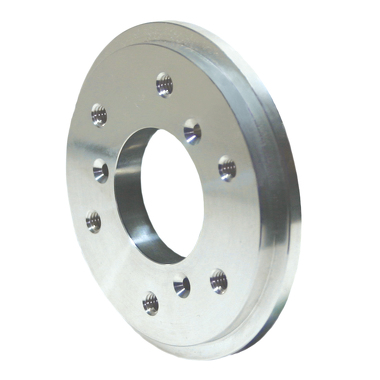
Flange, Ø 90mm
For shaft encoders with flange ø 50 ... 58 mmAdapter for converting a clamping flange into a synchro flange. Mechanically compatible with encoder type 9000.
Scope of delivery
- Flange adapter (aluminium)
- 3 screws for fastening to the encoder
Connection to the application (not included in delivery)
- 6 screws
8.0010.2270.0000 |
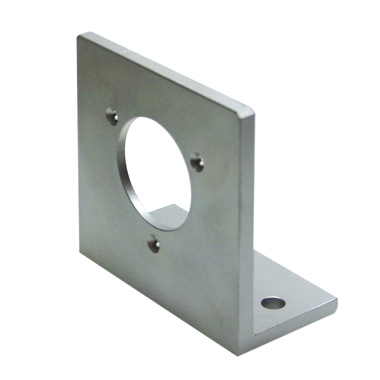
Angular flange
For shaft encoders with flange ø 50 ... 58 mmScope of delivery
- Angle flange (aluminium)
- 3 screws for fastening to the encoder.
Connection to the application (not included in delivery)
- 2 screws
8.0010.2300.0000 |
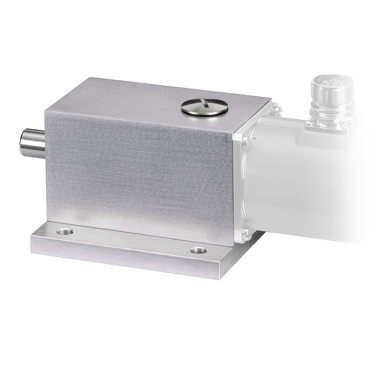
Bearing box
For shaft encoder with clamping flange ø 58 mm and shaft 10 x 20 mmWhen the encoder is driven by a toothed or chain wheel, V-belt or toothed belt, impeller, etc., the permissible axial or radial shaft loads are usually exceeded during operation. For these cases, the bearing box equipped with reinforced bearings is ideally suited.
Scope of delivery
- Bearing box with lock and O-ring
- Coupling for shaft 10 mm
- Adapter flange 8.0010.2100.0000
- Mounting accessories
8.0010.8200.0004 |
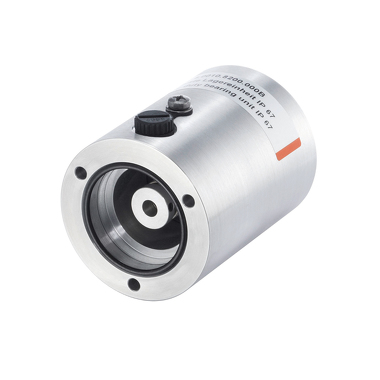
Robust bearing unit
For shaft encoders with clamping flange ø 50 ... 58 mm and shaft 10 mmThe separation of the bearing load and the sensor system provides the encoder with additional protection in harsh environments.
Scope of delivery
- Robust bearing unit
- 3 x cheese head screw M4x25 (SW3)
- 1 x O-ring
8.0010.8200.000C |
Cables and connectors
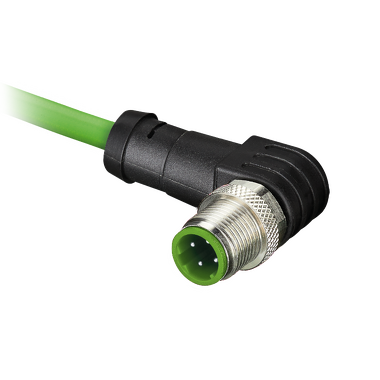
M12 Connector with cable , mit Edelstahl Überwurf
Preassembled cable set
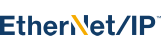
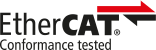
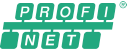
1 x 4 x AWG22 mm2